Linear Elastic Fracture Mechanics (LEFM)
Linear Elastic Fracture Mechanics (LEFM)
Strength v Toughness
The strength of a material is its resistance to plastic flow.  When a material is stretched under tensile loading or flexed as in 3 point bending, the yield strength or strength a break are important limiting factors or failure criteria.Â
The toughness, or better fracture toughness, is the resistance of a material to the propagation of a crack.  Linear Elastic Fracture Mechanics is the methodology used to predict or diagnose the failure of a part with an existing crack or flaw.
Although Charpy and Izod impact tests give toughness values for a material they do not give a true material property because the result depends on the sample geometry.  To get at the real material property that can be used in design calculation the stress intensity and fracture toughness is required.Â
Stress Intensity and Fracture Toughness
Stress Intensity and Fracture Toughness
The presence of a crack in a section under stress causes the local stress at the crack tip to increase as shown in Figure1. The material deforms as the local stress reached the material yield stress to form a plastic zone.  The size of the plastic zone depends on the material. A brittle fracture occurs where the plastic zone is small compared to the part thickness and ductile failure occurs when the plastic zone is large compared to the thickness.  For brittle fracture then linear elastic fracture mechanics (LEFM) can be used to determine the stress intensity factor.
In fracture mechanics, a stress intensity  factor (K1), is calculated as a function of applied stress (σ), crack size (c) and part geometry (geometry factor Y).  Failure occurs once the stress intensity factor exceeds the materials fracture toughness (K1c).  At this point the crack will grow in a rapid and unstable manner until fracture.
For mode 1 type failure where a tensile force acts to pull the crack faces apart, see Figure 1, K1 is given by: K1 =Y.σ.√(⫪.c)

Instrumented Falling Weight Impactor (IFWI)
Instrumented Falling Weight Impactor (IFWI)
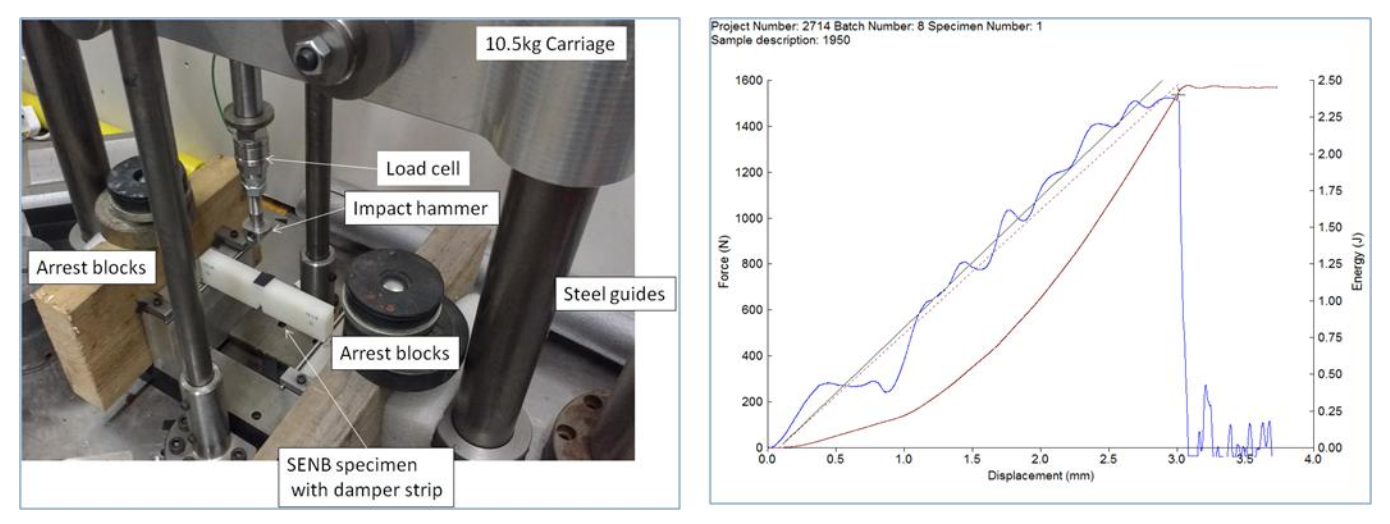
Impact Solutions have an Instrumented free falling weight system (IFWI) capable of impact energies of 450J and impact velocities of 4.5m/s currently fitted with a 20kN load cell, Figure 2.  Using this single edge notched specimens in 3 point bend configuration in accordance with BS ISO 17281:2002 we have used linear elastic fracture mechanics (LEFM) to obtain the K1c of a number of engineering polymers at 1m/s.  A typical load displacement curve for a PVDF polymer is shown in Figure 2.  The value of K1c in this case was 4.8MPa.m 0.5.